In over 30 years in the industry, I’ve sold almost every bond breaker that’s ever been made. Today, I’ll be sharing insights about bond breakers and tilt-up construction.
Introduction to Tilt-Up Construction
To begin, tilt-up construction can be best described as on-site precast. It has many advantages, notably, the flexibility of casting panels on-site rather than transporting them from a distant factory. Tilt-up is primarily used for buildings, not infrastructure. The panels can vary in size, from as small as 7×12 feet to massive ones weighing up to 162 tons.
Let me show you a visual of the tilt-up process.
Visual Demonstration of Tilt-Up
Here, we have a site where panels are being erected. Notice the crane on the right lifting a panel, showing how panels are moved into place. Once placed and anchored, structural steel is added for roofing. Tilt-up is efficient, and contractors aim to set as many panels as possible in a day.
Distinguishing Between Precast and Tilt-Up Panels
One significant distinction is between precast and tilt-up panels. Many precast buildings use fascia panels, which are not structural. In contrast, tilt-up panels are mostly structural. This advantage means fewer columns near the wall are needed, providing more structural support.
Another detail is about the joints between the panels. Typically, a non-sag urethane is used, with the panels usually kept 3/4 of an inch apart. This joint is sealed with a two-component polyurethane to ensure compatibility. A point to emphasize to clients is the advantage of using a complete system, ensuring compatibility and reducing the chance of complications.
The Role of Bond Breakers in Lifting
Now, when it comes to lifting these panels, the difference in bond breakers is evident. Watch closely. As they apply tension and lift the panel, it’s crucial that it rises smoothly, without any audible ‘pop’ or visible flex in the air. Achieving a smooth lift, especially with the amount of water underneath, is commendable. That’s the kind of quality SpecTilt delivers, resulting in such exemplary panels.
What is a Bond Breaker
A bond breaker, in the realm of tilt-up construction, is a material designed to prevent adhesion between freshly poured concrete panels and the casting surface they’re poured on. Think of it as a barrier – one that ensures the two surfaces don’t stick to each other. This barrier allows the concrete panel to be easily separated and lifted once it has cured. Essentially, it acts as an intermediary layer that ensures a smooth detachment process, facilitating efficient panel lifts without causing damage or imperfections.
Importance of Bond Breakers
Bond breakers play an indispensable role in tilt-up construction. First and foremost, their primary function ensures that panels remain undamaged during the lifting process. An efficient bond breaker ensures a clean, smooth lift without any unwanted adherence, resulting in pristine panel faces that reflect the hard-troweled, burned-in finish from the casting surface. Beyond the aesthetic value, bond breakers protect the structural integrity of the panels. A panel sticking to the casting surface during lifting can lead to cracks or deformations, undermining the panel’s strength and longevity. Additionally, bond breakers can save significant time and labor costs. Imagine the added effort and time it would take if every panel was sticking to its casting bed! Bond breakers expedite the construction process, ensuring projects stay on schedule and within budget.
Differences in Bond Breakers
Bond breakers come in various formulations, primarily distinguished by their base component: solvent-based or water-based. Historically, solvent-based bond breakers were the industry standard, recognized for their effectiveness. However, with environmental regulations and the rise in solvent prices, water-based bond breakers, like SpecTilt WB, have taken center stage. Thanks to advances in chemical engineering, today’s water-based bond breakers rival, if not surpass, their solvent-based counterparts in performance.
Another difference lies in their application and compatibility. Some bond breakers are better suited for certain surface finishes or environmental conditions. For instance, as you’ll see below, SpecTilt 100 or SpecTiltEX might be preferred during colder seasons due to their specific formulation. It’s essential to choose the right bond breaker for the job, factoring in the specific requirements of the project and the casting surfaces in use.
Best Bond Breakers for Tilt-Up Construction: SpecChem Product Line
Now, onto SpecChem Bond Breakers, starting with SpecTilt WB: it’s a standout in our lineup. Today, many of our products are water-based due to VOC regulations. Back when water-based bond breakers were first released, many preferred solvent-based, but formulation advances made water-based options just as effective, if not better. Plus, with solvent prices skyrocketing, the shift became economical. In colder seasons, many prefer SpecTilt 100 or SpecTiltEX due to cost-effectiveness.
SpecTiltWB has many benefits – it’s green, low VOC, and water-based. It also meets the moisture retention standards of ASTM C309 on steel trowel surfaces. The C309 standard is stringent, requiring minimal moisture loss during a 72-hour test, which SpecTiltWB meets. While it’s ideal for steel trowel floors, care is needed when used on rougher surfaces like casting slabs.
SpecChem’s Full Tilt-Up Bond Breaker Product Line
Here’s a comprehensive look at SpecChem’s line of Tilt-Up Bond Breakers:
Tilt-up construction demands precision and quality in every step, and one can’t emphasize enough the significance of an effective bond breaker. SpecChem, known for its meticulous product engineering, offers a range of bond breakers tailored to the unique requirements of tilt-up projects.
1. SpecTilt WB
Type: Premium reactive water-based tilt-up cure/bond breaker.
Description: Specially engineered to ensure a smooth lift of tilt-up panels, SpecTilt WB adheres strictly to ASTM C309 moisture retention standards. Unlike many other bond breakers, it contains no diesel, kerosene, waxes, or silicones.
Features & Benefits:
- Chemically reactive formula ensures optimal results.
- VOC-compliant, coming in at less than 350g/l.
- Robust against foot traffic abrasion.
- Panels lift cleanly with no resin stains.
2. SpecTilt 100
Type: Premium reactive solvent-based tilt-up bond breaker.
Description: Designed with a reactive chemical formula, SpecTilt 100 ensures tilt-up panels lift effortlessly, leaving behind no residues, stains, or discolorations. This solution is free of diesel, kerosene, waxes, and silicones.
Features & Benefits:
- Leaves panels immaculate with no residues or discolorations.
- Resistant to abrasions from foot traffic.
- Ensures clean lifts with no resin stains.
3. SpecTilt EX
Type: Quick-drying reactive VOC/OTC-compliant solvent-based bond breaker.
Description: Tailored for areas that require VOC compliance, like the OTC/LADCO/MRPO regions, SpecTilt EX combines the efficiency of a solvent-based bond breaker with rapid drying capabilities. Especially beneficial for cool, damp climates.
Features & Benefits:
- Chemically reactive, ensuring consistent results.
- Fast drying to boost productivity in unfavorable climates.
- High resistance against foot traffic wear.
- Clean panels: devoid of residue, stains, or discoloration.
- OTC/VOC-compliant with less than 350 g/l.
4. Clean Lift 20/20
Type: Premium reactive water-based tilt-up cure/bond breaker.
Description: Created for a seamless lift of tilt-up panels, Clean Lift 20/20 abides by the ASTM C309 standards for moisture retention. It’s formulated without diesel, kerosene, waxes, or silicones, ensuring purity and performance.
Features & Benefits:
- VOC-compliant, registering less than 350 g/l.
- High resilience against foot traffic abrasion.
- Distinctive appearance on the casting slab, allowing for easy identification.
- Ensures panels lift cleanly, free from resin stains.
When the discussion veers towards the ideal bond breakers for tilt-up construction, SpecChem’s array of products stands out. The brand’s commitment to quality, innovation, and performance is evident in every bond breaker, ensuring contractors can achieve impeccable results every time.
Importance of Panel Finish
Looking at these panels, they haven’t undergone much preparation. They’ve been set in place and the excess reveal strips have been removed. But, they’re largely unchanged since their lifting. What construction experts aim for are panels with tight faces, mirroring the floor beneath. If the floor is a hard-troweled, burned-in finish, the panel should mimic that finish, maintaining that tight, smooth look.
Variations in Panel Placement
If you notice the panels placed atop others within the building, they are lifted from the top, allowing for ‘plumb setting.’ This means the panel is positioned perfectly vertically when set in place. Unlike the first video where the panel was lifted from its face…
You’ll notice these panels are set at an angle due to the way they’re lifted from the face. However, by pulling from the edge, it allows a direct set down, eliminating the need for adjustments and braces.
Evolution of Panel Finishes
While most panels today have flat faces, there’s a rich history in panel finishes. I remember an old tilt-up building from my early days, featuring an exposed aggregate tilt-up. They embedded large rocks in the casting bed and then poured concrete over it. Modern panels even have brick designs where thin bricks are laid out.
Advantages of SpecChem’s Tilt-Up System
One of our key strengths lies in our comprehensive system. It might be challenging to get tilt-up contractors to shift, but with our proven track record, we offer single-source liability.
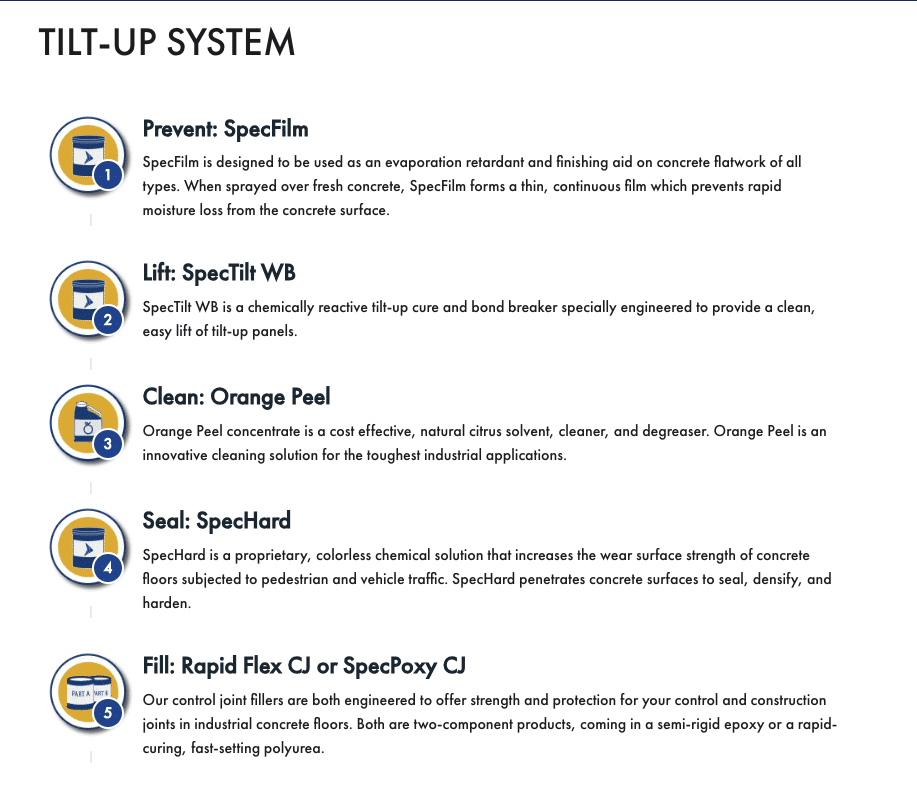
It’s often said that the sum is greater than its parts, and that’s certainly true when you consider SpecChem’s comprehensive Tilt-Up System. Our approach isn’t about offering standalone products; it’s about delivering an integrated solution that covers every phase of the tilt-up process. Here’s why our systems, not just our products, hold the advantage:
- Seamless Integration: Every product in our Tilt-Up System has been meticulously designed to complement the others. Each component naturally transitions to the next. This means no more mismatched products, reduced chances of incompatibility, and a smoother construction journey from start to finish.
- Single-Source Reliability: By sourcing your entire tilt-up suite from SpecChem, you’re placing your trust in a single, reputable brand. This eliminates the challenges of dealing with multiple suppliers or worrying about the compatibility of products from different manufacturers. We stand behind our complete system, offering not only quality products but peace of mind.
- Consistent Quality: Consistency is key in construction. By using our integrated system, you ensure that every step of the process is backed by SpecChem’s unwavering commitment to quality. Whether it’s the clean lift from SpecTilt WB or the enhanced wear surface strength from SpecHard, our consistency in performance is unmatched.
- Cost-Effective: Time is money in the construction industry. Our system minimizes the trial and error of mixing products from various suppliers, ensuring optimal performance and reducing costly delays. Plus, with products like Orange Peel, which offers a cost-effective cleaning solution, you’re sure to get the best value for your money.
- Complete Solution: Think of our Tilt-Up System as a toolkit – you wouldn’t want to miss any tool when tackling a project. From preventing moisture loss to sealing and protecting the finished panel, we’ve got you covered at every stage. It’s not just about selling products; it’s about providing a comprehensive solution to ensure your tilt-up construction is a resounding success.
In a landscape where every detail matters, why leave anything to chance? SpecChem’s Tilt-Up System provides an integrated, reliable, and efficient solution for all your tilt-up needs. When you choose our system, you’re not just choosing products; you’re choosing success, consistency, and peace of mind.